Revolutionizing Heavy Machinery Service Flow and Tracking with IoT
Revolutionizing Heavy Machinery Service Flow and Tracking with IoT
OneIoT
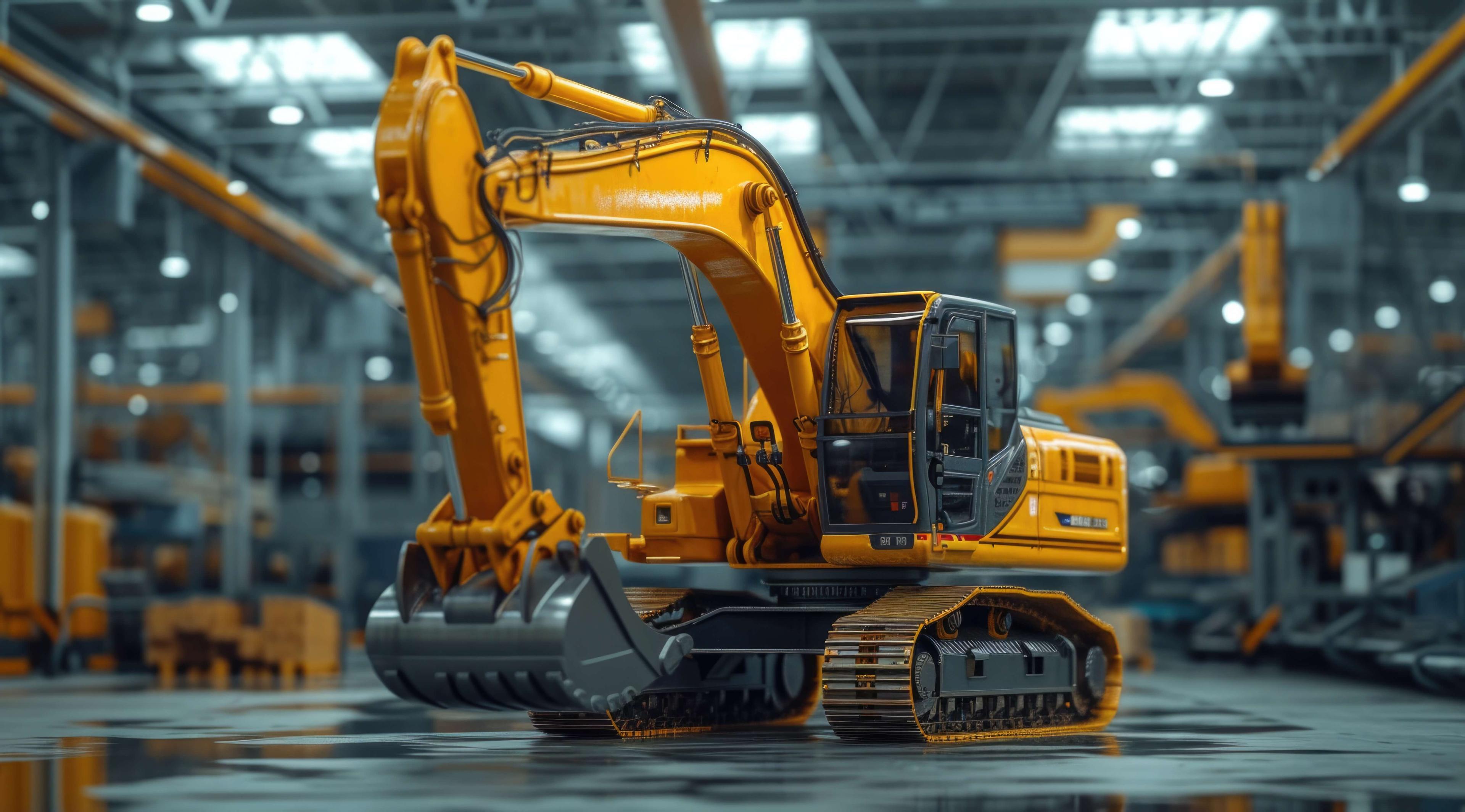
Heavy machinery service centers often grapple with a host of challenges that can hinder operational efficiency and customer satisfaction. These challenges include inefficient equipment tracking, lack of yard visibility, manual workflows, and the need for automation. OneIoT offers a comprehensive solution to address these pain points and streamline the entire service and delivery process.
The Challenges
- Inefficient Equipment Tracking: Difficulty in locating equipment promptly can lead to significant delays and increased costs.
- Lack of Yard Visibility: Limited visibility into equipment utilization and idle time can hinder resource optimization.
- Manual Workflows: Manual processes are time-consuming, error-prone, and often lack transparency.
- Need for Automation: Automating workflows can improve efficiency, reduce human error, and enhance overall productivity.
OneIoT's Solution: A Comprehensive Approach
OneIoT's solution leverages IoT technology to provide real-time visibility and automation throughout the entire service flow.
Real-Time Equipment Tracking
- GPS/BLE Tracking: Each piece of heavy machinery is equipped with a GPS/BLE device that enables accurate tracking of its location.
- Live Location Visualization: A user-friendly map interface provides real-time visualization of the location of each machine.
- Geo-fencing Alerts: Automated alerts are triggered when a machine enters or exits predefined geofenced areas.
Workflow Automation
- JCB Entry and Initial Tracking:
- Upon entry, a GPS tracker is automatically provisioned to the machine.
- A service incident is created and assigned to the service engineering team.
- Relevant team members are notified via email, MS Teams, or other preferred channels.
- Service and Repair:
- The service engineer is assigned to the incident.
- Work progress is tracked and updated in real-time.
- Upon completion, the engineer closes the incident.
- Quality Check:
- A quality check incident is automatically generated.
- The quality check team is assigned to inspect the machine.
- The quality check is completed and the incident is closed.
- Dispatch and Delivery:
- A dispatch ticket is automatically created.
- The delivery team receives the ticket and initiates the delivery process.
Monitoring and Visualization
OneIoT's platform provides powerful monitoring and visualization tools:
- Customizable Dashboards: Create tailored dashboards to visualize key metrics and KPIs.
- Real-Time Location Tracking: Monitor the real-time location of each machine.
- Geofencing Alerts: Receive alerts for unauthorized movement or idle time.
- Equipment Status Tracking: Monitor the status of each machine, including its current location, assigned engineer, and service history.
Notification System
OneIoT's notification system ensures timely communication and transparency:
- Customizable Notification Channels: Receive notifications via email, SMS, or push notifications.
- Real-Time Alerts: Stay informed about critical events, such as equipment breakdowns or service completion.
- Status-Based Notifications: Receive notifications based on specific status changes.
- Targeted Notifications: Send notifications to specific individuals or groups.
By leveraging IoT technology, OneIoT's solution offers a comprehensive approach to heavy machinery service flow and tracking. It improves efficiency, reduces downtime, and enhances overall operational visibility. With real-time data, automated workflows, and advanced analytics, OneIoT empowers businesses to make informed decisions and optimize their operations.